Datasheet TMC4671 (TRINAMIC) - 42
Производитель | TRINAMIC |
Описание | Dedicated Motion Controller for 2-/3-Phase PMSM |
Страниц / Страница | 159 / 42 — Info. 4.7.10.3 Encoder Initialization by Hall sensors. 4.7.10.4 Encoder … |
Формат / Размер файла | PDF / 5.1 Мб |
Язык документа | английский |
Info. 4.7.10.3 Encoder Initialization by Hall sensors. 4.7.10.4 Encoder Initialization by N Pulse Detection
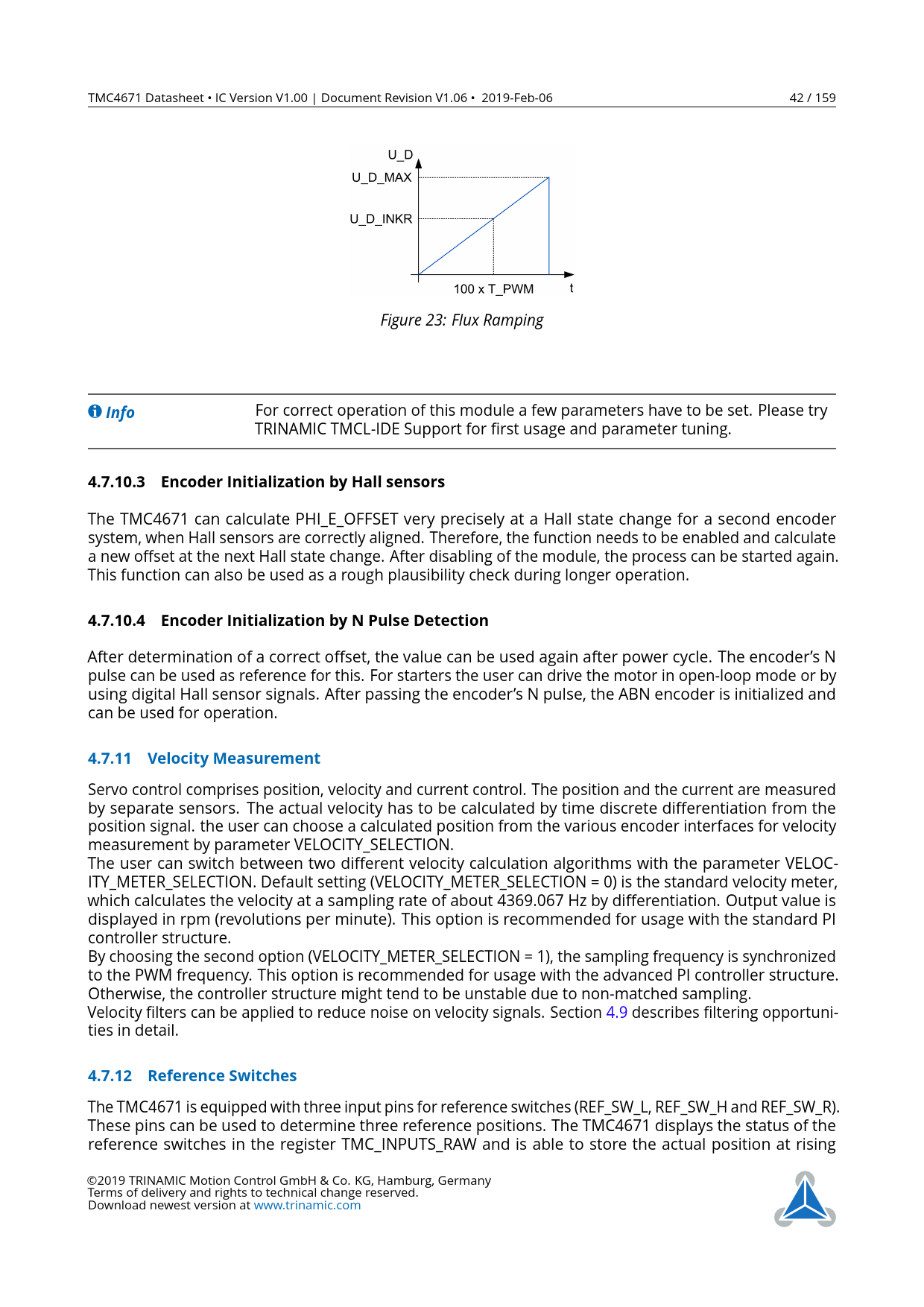
Модельный ряд для этого даташита
Текстовая версия документа
link to page 49 TMC4671 Datasheet • IC Version V1.00 | Document Revision V1.06 • 2019-Feb-06 42 / 159 Figure 23: Flux Ramping
Info
For correct operation of this module a few parameters have to be set. Please try TRINAMIC TMCL-IDE Support for first usage and parameter tuning.
4.7.10.3 Encoder Initialization by Hall sensors
The TMC4671 can calculate PHI_E_OFFSET very precisely at a Hall state change for a second encoder system, when Hall sensors are correctly aligned. Therefore, the function needs to be enabled and calculate a new offset at the next Hall state change. After disabling of the module, the process can be started again. This function can also be used as a rough plausibility check during longer operation.
4.7.10.4 Encoder Initialization by N Pulse Detection
After determination of a correct offset, the value can be used again after power cycle. The encoder’s N pulse can be used as reference for this. For starters the user can drive the motor in open-loop mode or by using digital Hall sensor signals. After passing the encoder’s N pulse, the ABN encoder is initialized and can be used for operation.
4.7.11 Velocity Measurement
Servo control comprises position, velocity and current control. The position and the current are measured by separate sensors. The actual velocity has to be calculated by time discrete differentiation from the position signal. the user can choose a calculated position from the various encoder interfaces for velocity measurement by parameter VELOCITY_SELECTION. The user can switch between two different velocity calculation algorithms with the parameter VELOC- ITY_METER_SELECTION. Default setting (VELOCITY_METER_SELECTION = 0) is the standard velocity meter, which calculates the velocity at a sampling rate of about 4369.067 Hz by differentiation. Output value is displayed in rpm (revolutions per minute). This option is recommended for usage with the standard PI controller structure. By choosing the second option (VELOCITY_METER_SELECTION = 1), the sampling frequency is synchronized to the PWM frequency. This option is recommended for usage with the advanced PI controller structure. Otherwise, the controller structure might tend to be unstable due to non-matched sampling. Velocity filters can be applied to reduce noise on velocity signals. Section 4.9 describes filtering opportuni- ties in detail.
4.7.12 Reference Switches
The TMC4671 is equipped with three input pins for reference switches (REF_SW_L, REF_SW_H and REF_SW_R). These pins can be used to determine three reference positions. The TMC4671 displays the status of the reference switches in the register TMC_INPUTS_RAW and is able to store the actual position at rising ©2019 TRINAMIC Motion Control GmbH & Co. KG, Hamburg, Germany Terms of delivery and rights to technical change reserved. Download newest version at www.trinamic.com Document Outline 1 Order Codes 2 Functional Summary 3 FOC Basics 3.1 Why FOC? 3.2 What is FOC? 3.3 Why FOC as pure Hardware Solution? 3.4 How does FOC work? 3.5 What is Required for FOC? 3.5.1 Coordinate Transformations - Clarke, Park, iClarke, iPark 3.5.2 Measurement of Stator Coil Currents 3.5.3 Stator Coil Currents I_U, I_V, I_W and Association to Terminal Voltages U_U, U_V, U_W 3.5.4 Measurement of Rotor Angle 3.5.5 Measured Rotor Angle vs. Magnetic Axis of Rotor vs. Magnetic Axis of Stator 3.5.6 Knowledge of Relevant Motor Parameters and Position Sensor (Encoder) Parameters 3.5.7 Proportional Integral (PI) Controllers for Closed Loop Current Control 3.5.8 Pulse Width Modulation (PWM) and Space Vector Pulse Width Modulation (SVPWM) 3.5.9 Orientations, Models of Motors, and Coordinate Transformations 4 Functional Description 4.1 Functional Blocks 4.2 Communication Interfaces 4.2.1 SPI Slave User Interface 4.2.2 TRINAMIC Real-Time Monitoring Interface (SPI Master) 4.2.3 UART Interface 4.2.4 Step/Direction Interface 4.2.5 Single Pin Interface 4.3 Numerical Representation, Electrical Angle, Mechanical Angle, and Pole Pairs 4.3.1 Numerical Representation 4.3.2 N_POLE_PAIRS, PHI_E, PHI_M 4.3.3 Numerical Representation of Angles PHI 4.4 ADC Engine 4.4.1 ADC Group A and ADC Group B 4.4.2 Internal Delta Sigma ADCs 4.4.3 External Delta Sigma ADCs 4.5 Delta Sigma Configuration and Timing Configuration 4.5.1 Internal Delta Sigma Modulators - Mapping of V_RAW to ADC_RAW 4.5.2 External Delta Sigma Modulator Interface 4.5.3 ADC Configuration - MDAC 4.6 Analog Signal Conditioning 4.6.1 FOC3 - Stator Coil Currents I_U, I_V, I_W and Association to Terminal Voltages U_U, U_V, U_W 4.6.2 Stator Coil Currents I_X, I_Y and Association to Terminal Voltages U_X, U_Y 4.6.3 ADC Selector & ADC Scaler w/ Offset Correction 4.7 Encoder Engine 4.7.1 Open-Loop Encoder 4.7.2 Incremental ABN Encoder 4.7.3 Secondary Incremental ABN Encoder 4.7.4 Digital Hall Sensor Interface with optional Interim Position Interpolation 4.7.5 Digital Hall Sensor - Interim Position Interpolation 4.7.6 Digital Hall Sensors - Masking and Filtering 4.7.7 Digital Hall Sensors together with Incremental Encoder 4.7.8 Analog Hall and Analog Encoder Interface (SinCos of 0° 90° or 0° 120° 240°) 4.7.9 Analog Position Decoder (SinCos of 0°90° or 0°120°240°) 4.7.10 Encoder Initialization Support 4.7.11 Velocity Measurement 4.7.12 Reference Switches 4.8 FOC23 Engine 4.8.1 PI Controllers 4.8.2 PI Controller Calculations - Classic Structure 4.8.3 PI Controller Calculations - Advanced Structure 4.8.4 PI Controller - Clipping 4.8.5 PI Flux & PI Torque Controller 4.8.6 PI Velocity Controller 4.8.7 P Position Controller 4.8.8 Inner FOC Control Loop - Flux & Torque 4.8.9 FOC Transformations and PI(D) for control of Flux & Torque 4.8.10 Motion Modes 4.8.11 Brake Chopper 4.9 Filtering and Feed-Forward Control 4.9.1 Biquad Filters 4.9.2 Standard Velocity Filter 4.9.3 Feed-Forward Control Structure 4.10 PWM Engine 4.10.1 PWM Polarities 4.10.2 PWM Frequency 4.10.3 PWM Resolution 4.10.4 PWM Modes 4.10.5 Break-Before-Make (BBM) 4.10.6 Space Vector PWM (SVPWM) 5 Safety Functions 5.1 Watchdog 6 Register Map 6.1 Register Map Overview 6.2 Register Map Full 7 Pinning 8 TMC4671 Pin Table 9 Electrical Characteristics 9.1 Absolute Maximum Ratings 9.2 Electrical Characteristics 9.2.1 Operational Range 9.2.2 DC Characteristics 10 Sample Circuits 10.1 Supply Pins 10.2 Clock and Reset Circuitry 10.3 Digital Encoder, Hall Sensor Interface and Reference Switches 10.4 Analog Frontend 10.5 Phase Current Measurement 10.6 Power Stage Interface 11 Setup Guidelines 12 Package Dimensions 13 Supplemental Directives 13.1 Producer Information 13.2 Copyright 13.3 Trademark Designations and Symbols 13.4 Target User 13.5 Disclaimer: Life Support Systems 13.6 Disclaimer: Intended Use 13.7 Collateral Documents & Tools 14 Errata 15 Figures Index 16 Tables Index 17 Revision History 17.1 IC Revision 17.2 Document Revision